|
|
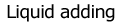 |
|
|
 |
Liquid
Adding System |
In
modern industry process, adding liquid on powder happens a lot.
Non gravity mixer can add liquid with wide range of viscosity
and oil or wax type, and especially it is excellent effect in
oil coating. The method to add liquid to powder is divided into
active input and passive input, and according to the physical
properties of powders or liquids, the design condition differs. |
|
Design
condition |
absorption
capacity of powder size
of particles of powder viscosity
and input amount of liquid |
|
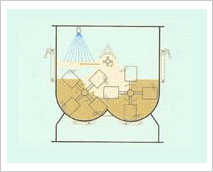 |
F.D,B
System
IIn case of adding liquid to powder, there is a tendency
for materials to get crushed. To prevent this agglomeration,
it maximizes the uniformity of material with F.D.B. It
is high-speed body of revolution, and stimulates uniform
connection between powder and liquid through forming material
film on higher part of mixing room. |
|
|
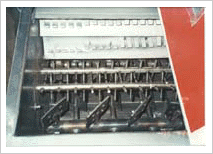 |
Pin Mill System
In case of mixing powder that requires particle crushes
by shearing, Pin Mill System is consisted with fixed cover
attached with Pin on two F.D.B. When adding liquid, in
case of material with strong self cohesion and hygroscopicity,
the best uniform mixture can be obtained. |
|
|
n case that powder
particle is finer than liquid (No more than 10), the agglomeration
of material increases greatly, so you should be careful
in liquid particles than powder. N.P.C(New Power Crushe)
is high speed body of revolution that crushes blocked
materials or crystal of powder particles, it can contribute
to the simplifying work of complicated industrial process. |
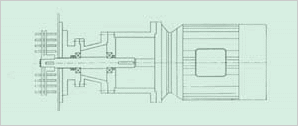 |
|
|
Study
on segregation phenomena and attachment prevention in mixing
particles |
In
mixing process of most feed and food, the quality of mixing
can be raised by clearing segregation in the course of mixing
by binding particles to coarse particle by adding sticky liquid
such as Vegetable oil, Fat, Molasses. This method of adding
binder to liquid type can be applied in mixing powder in feed
as well as overall industry.
However, this sticky liquid breaks up mixing process by building
up material by sticking to casing part of mixer. However please
concentrate on that these problems can be solved with proceeding
way of mixing, operation of equipment and design, and Non
gravity mixer solves the problems (attachment of material,
breakage, and heat generation etc) when adding liquid on the
basis of unique technology and experience.
|
|
 |
Most feed is divided into various sizes
of particles, and differences in diameter and density cause
segregation during the course of mixing. In this case particles
has characteristics that are not mixed well by uniting themselves. |
|
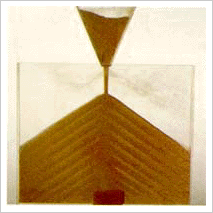 |
For example, in case of Selenium, it is
input to most feeds by 0.4ppm(0.4gr/ton), and in case
that 10 times of standard amount, so as to 4ppm is input
into a part of feed without being mixed uniformly, the
animal that is feed this can meet a serious problem.
Therefore, this kind of diffusion (also, mixture) of particle
atom such as selenium should be done very delicately,
and to overcome this problem even partly, before performing
main mixing, sometimes pre-mixing is done such as minerals
and vitamins. In these cases, also, the particles of premix
should be mixed perfectly with mesh feed.
|
|
|
Even after finishing this mixing, danger
about segregation is continued, and the emission of material
is important too. Among this emission, to prevent segregation
phenomenon, emission should use "Bottom Drop" or "Bottom Door"
method. Also, even when filling mesh feed or unpelled material
into silo, you should pay attention to segregation, and the
most important thing is that you should not fill materials in
shape of corn or hill.
If material is filled in corn shape, material¡¯s particles flocks
in the center according to the difference in density and diameter,
it is filled in tree shape, and the flow of materials becomes
cone flow or central flow, and also the material of central
post would come out first. In this core part, only the density
of premix becomes high, and although the amount of medicines
and minerals is not fetal, it can make some limitations in activity
of animals. |
|
 |
As
a method to prevent segregation of particles in feed mixture,
there is an addition of a binder such as oil or molasses into
materials.
This makes relatively fine particle in mixture to attach on
big particle by coating the surface of relatively big particle
and making it sticky. Then when dumping to silo, it can prevent
segregation as minute particle drops in condition of sticking
to big particle. It was proved that it is saved as more uniform
mixture than the mixture that sticky liquid is not added in
saved condition through several experiments.
Kansas state university of America confirmed the advantage of
mixing effect in sticky liquid(Sticky Liquid, Binder). However,
the problems so far are to add liquid not to built up more in
mixer when adding and mixing other liquids such as molasses
or solidified fat, and vegetable oil etc. If this case happens,
mixing would happen partly, but it would lose the function as
overall mixer. |
|
 |
Now
a premix manufacturing company in a foreign country is adding
molasses as binder into ribbon mixer, and in the ribbon mixer,
mixing happens in the backside of ribbon as the principle in
other ribbon mixer.
At this time, the problem is molasses and mixture becomes like
wing of airplane by attaching on the back of ribbon, and after
some hours, mixer stopped mixing, and the production chief input
2 persons to clean the mixer for two hours for only few hours
mixing work. Also as the company uses limestone as premix excipient,
abrasion on ribbon is so serious. The task of the Norway company
is to add sticky liquid into mixer, not damaging the function
of the machine.
On the other hand, a premix manufacturer in Denmark who use
¡°Non gravity mixer¡± to add similar amount of molasses cleans
only once in a week to prevent the material to be built up in
mixer. The mixing in ¡°Non gravity mixer¡± is happening at the
center not happening at the edge like ribbon mixer, even though
molasses are built up in paddle, it does not break up the mixing.
Relatively big amount of molasses can be added, and the best
solution to minimize to build up in ¡°Non gravity mixture¡± is
in the picture 1. According to this solution, to prevent direct
spraying of molasses or binder on paddle system, Flow Distortion
Bar (F.D.B) sprays material towards body before liquid sticks
to mixer, and it prevents material from sticking or caking on
the wall or other part greatly.
In case of Molasses, it is usually added by spray automization,
and there are two ways to spray in most effective way.
Firstly, to ease automization by increasing fluency by heating
molasses.
Secondly, there is a way to dilute molasses with 10% water,
and the better spray nozzle diffuses, the better material is
absorbed unto mixer without being built up. However, to diffuse
and mix sticky liquid in the most effective way, other operation
besides general operation is needed.
The first solution is to over-fill 40% into mixer. For example,
2,000L ¡°Non-gravity mixer¡± is general feed material, and should
load material with 1.2 ton, and in this case, mixing time and
mixing cycle get longer a little. These over time is differentiated
according to the amount of liquid, and if you want to only bind
or interlock small particle and large particle, it is possible
with only approximately 2% of liquid. At this time, it takes
about 90sec for mixing including filling, mixing, liquid adding
and emission.
In this case, the theological amount of mixer is 48ton/hr, and
to get his productivity, it is required to divide dosing system
into 3 or 4 at least not measuring with a big scale. This method
can measure more accurately as it can measure in small unit.
The technology to prevent direct spraying of mixer¡¯s liquid
through flowing is helpful to diffuse relatively small particle
and liquid in mixture perfectly.
Also, the material such as limestone(bigger particle than about
850) that is crushed into relatively big particle has so big
¡°internal friction¡± during the overall process of mixing, it
seems to be able to spray directly to mixer without F.D.B, but
as it has so big interior friction force, it should increase
power when adding driving force or sticky liquid. No material
has problem in mixing within ¡°Non gravity mixer¡±.
However, the important thing is how to add liquid not to stick
to wall or other parts, and if it can be solved, more than two
nozzles can be used. |
|
 |
The
limitation in adding molasses into mixer depends on the absorption
ability of mixture about molasses, and if molasses has relatively
big particle as pellet, the particle becomes sticky easily.
However, in case of particle, the smaller is particle, the bigger
the surface area becomes. So the absorption ability on the surface
of particle would become high. In case of most feed, the relatively
minute particle of mixed material can absorb relatively high-density
sticky liquid. However, in case of high density, more time is
required to mix, therefore, productivity can be reduced.
Now, for pellet press, ¡°Non-gravity mixer¡± that mixes by adding
7% molasses in mesh or meal are being used a lot. If you would
like only to bind the particle of mixture to improve the stability
of product, it is possible only adding 2% molasses, and ¡°Non
gravity¡± is used a lot for this usage. In any cases, it is important
how to operate sticky liquid to improve the final quality or
overall function of mixer. |
|
 |
As
discussed in advance, there are several elements to obstruct
uniform mixing in mixing process. And among those, the difference
in density and diameter are divided into the most important
factor.
Also when adding liquid, the problems of solidification of material
by viscosity that was serious before, and other problems such
as mechanical loading, cleaning, and maintenance of machine
are becoming serious problems in powder mixing in several industrial
fields as well as feed industry.
These problems can be solved perfectly how to operate and mix
liquid. We are certain that ¡°Non gravity mixer¡± would solve
these problems with rich technology and experience. |
|
|
|
|
|
|