|
 |
|
|
 |
The
two axes of mixing interior rotates to different sides and paddles
attached to the axes forms fluidized area by diffusing mixed
materials to different directions according to stable apex speed.
|
|
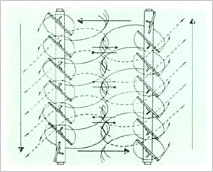 |
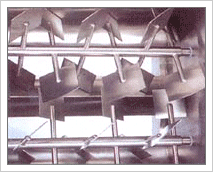 |
[moving direction of materials] |
[arrangement of plates] |
|
|
At
this time, the movement of materials is concentrated on the
higher center part from the bottom of mixer, and therefore,
the effective volume of mixing room increases, and as the effective
volume increases, the collision and rubbing between materials
decrease.
Also, as the contacting section between materials and the mixing
room, there is no damage because of collision and rubbing, and
on the other hand, mixer itself does not cause inner rubbing
because of material, so it keeps the shape of particle, and
as it does not press rotating object or ventless etc., it prevents
the leakage of materials on the seal part and proceed mixing. |
|
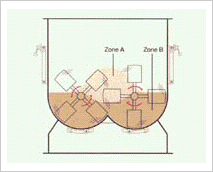 |
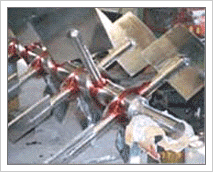 |
[mixing field and transfer field] |
[formation of plates] |
|
|
Like
this, Non-gravity mixer became created the new concept of powder
mixing by solving problems of eruption and leakage etc, as well
as precision of mixing. |
|
 |
1.
The fluidized Zone Mixing |
By
forming a fluidized zone in the mixing room, it proceeds rapid
mixing in a Non-gravity condition regardless of diameter of
materials, specific gravity, and shape |
|
2.
Homogeneous Mixing |
By
diffusing and moving materials in actiniform by the dynamic
structure of paddle, it mixes small adding agent even in mass
ratio of 1:100,000. |
|
3.
Gentle Mixing |
As
the speed of rotation axis is slow, the impact or shearing force
on material is not caused. So it can proceed mixing without
damaged materials. |
|
4.
Short Mixing Time |
In case of powder mixing, the time that takes to mix is so short,
and it takes less than 1 minute and only in a few seconds. |
|
5.
Economical Mixing |
As
it proceeds mixing in a short time, it reduces operation cost
and maximize productivity at the same time, and also mass production
with small-scale equipment. Therefore, initial installation
charge and driving cost are low. |
|
 |
All
mixers have its own effective space that material can move within
the mixer. Generally, half of total volume of a mixer is called
as working capacity, and it decides the unit productivity of
a mixer.
Like this, the unit productivity of the mixer forms an axis
of production process, and it is the index to measure total
productivity.
However as modern industry becomes more diversified and accurate,
mixers also became require elasticity in fixed space, and
the Non gravity mixer can produce products in the most effective
way in small space responding to the expectation of this production
process. |
|
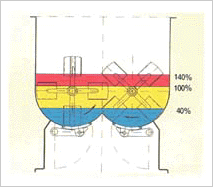 |
In case of using
.D.B or P.M.S, it is desirable to fill more than 120%
of materials, and the amount to fill that can be mixed
is MAX.140%,MIN 40% as the picture.
In case of mixing beyond the range, please contact
and ask to us. Also F-100 that is shown in dimension
of this Non gravity mixer is indication of working
volume that can be actually mixed.
Full volume is almost 2 times of working volume. Also
as indicated in volume, the value multiplying bulk density
of a material is conversed to Kg. |
|
|
|
|
|
|
|
|