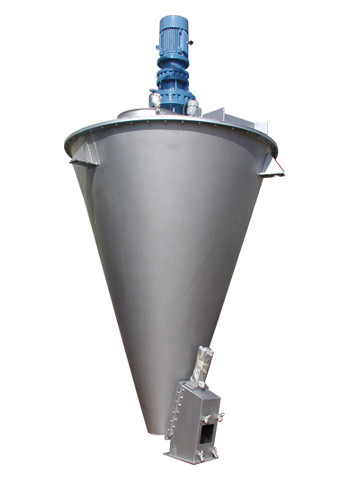
Double Screw Mixer (hereinafter referred to as DS Mixer) is a paired helical&conical mixer. This DS Mixer is the newest and best paired helical asymmetric mixer that has adopted the cutting edge technology of the United States and the excellent mixer technology of advanced countries such as Germany and Japan. The efficiency of this device is twice that of a single helical mixer and has a mixing effect of more than 10 times that of grating type mixer and is highly adaptable to differenttypes of mixture. The advantages of this mixer are as follow:
- Due to the flexibility of low-speed mixing, there is no risk of overheating for heat-sensitive materials and no layer is formed when mixing materials with different proportions and sizes of granules.
- Since the rotating speed of arm and pitch are pre-set, and the forces of rotation and revolution are mutually considered, the mixture is not crushed or damaged during mixing. The mixture is not deposited anywhere inside the device and the mixing precision is very high.
- Since the mixing is of low speed, it is possible to use vacuum processes and have low noise, beautiful appearance, simple structure. It is easy to clean, and cleaning solutions are not left inside the device after cleaning.
- The structure is simple and easy to operate. It is easy to maintain and takes only a little bit of space.The mixing process is done very fast despite of the low speed of device (typically takes about 5-7 minutes).
- When the materials to mix require addition of liquid during mixing or contain large amount of arsenic acids, the user can add liquid or attach the spraying system. Indeed, it is a state-of-art mixer mainly supplied to chemical industry companies.
DS Mixer is used in production processes in industries such as chemical, fertilizer, agrochemical, dye, feed, metallurgy, food, plastic, cement and ceramics industries. The mixer is widely used in mixing raw materials in the form of powder + powder, powder + liquid, granule + liquid, etc.
D.S Mixer rotates a pair of mutually asymmetric screws within the inverted conical container, while simultaneously revolving them.
Please refer to Figure 1 and Figure 2. Combine the movements of Diagram A, B, C of Figure 3 to them. The principle of mixing is an efficient process that mainly centers around convective mixing.Rotation: Due to the rotation of the primary and secondary screws, the raw materials are conveyed upwards along the wall of the vessel and are sprayed to the surroundings. Revolution: The screw revolves and rotates at the same timeand mixes the raw materials while applying horizontal circular motion. Gravity: Since the raw materials areconveyed upwards along the wall of the device, space is formed in the lower part of the device. Raw materialsthat did not pass through the screws drop down to the downward empty space due to the force of gravity.
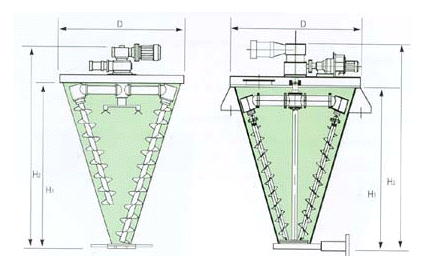
DS-0.3 | DS-0.5 | DS-1 | DS-1.5 | DS-2 | DS-3 | DS-4 | DS-6 | |
---|---|---|---|---|---|---|---|---|
󸮷®( t/h ) | 0.3-1 | 0.5-1.5 | 2-3 | 3-4.5 | 2.5-6 | 5-7.5 | 5-10 | 7-12 |
¿ë±â°æD1(¥õ) | 856 | 1062 | 1535 | 1560 | 1890 | 2130 | 2200 | 2450 |
H1 | 1022 | 1355 | 1723 | 2000 | 2310 | 2530 | 2922 | 3160 |
Ãⱸ°æ | 225 | 225 | 300 | 300 | 300 | 390 | 390 | 440 |
D | 936 | 1142 | 1610 | 1700 | 1970 | 2210 | 2280 | 2740 |
H | 1670 | 2000 | 2520 | 2800 | 3130 | 3550 | 3940 | 4720 |
°øÀüRPM | 2 | 2 | 2 | 2 | 2 | 2 | 2 | 2 |
ÀÚÀüRPM | 140 | 120 | 60 | 60 | 60 | 60 | 60 | 60 |
Áß·®(KG) | 550 | 600 | 1200 | 1500 | 1500 | 2100 | 2750 | 3500 |
The designed proportion of product is assumed to be 0.6.
The mixture throughput varies depending on the input methods of the raw materials and the discharge methods of the product.